When you’re running an industrial facility in St. Charles, your flooring isn’t just a surface—it’s a critical part of your operation. Whether it’s forklifts zipping through loading zones or massive equipment parked on concrete for hours at a time, your floor takes a beating. So it’s only natural to ask: can epoxy flooring handle heavy machinery and forklifts in St. Charles?
The short answer is yes—but only if it’s done right. Epoxy flooring has a reputation for strength, and with the right preparation, materials, and installation methods, it can absolutely stand up to the demands of industrial work. That’s why facilities across St. Charles rely on STL Coatings for custom flooring solutions built for load, traffic, and long-term performance.
Understanding Epoxy’s Load Capacity
Let’s start with the basics. Epoxy coatings are made by mixing resin and hardener, which chemically bond to form a hard, dense surface over concrete. This bond creates a rigid system that resists wear, impact, chemicals, and—most relevant here—extreme weight.
When installed over structurally sound concrete, epoxy coatings can easily support the pressure from heavy machinery, pallets, and forklifts without cracking or peeling. In fact, 100% solid epoxy flooring systems can support loads of up to several thousand pounds per square inch (PSI) depending on the coating thickness and concrete condition underneath.
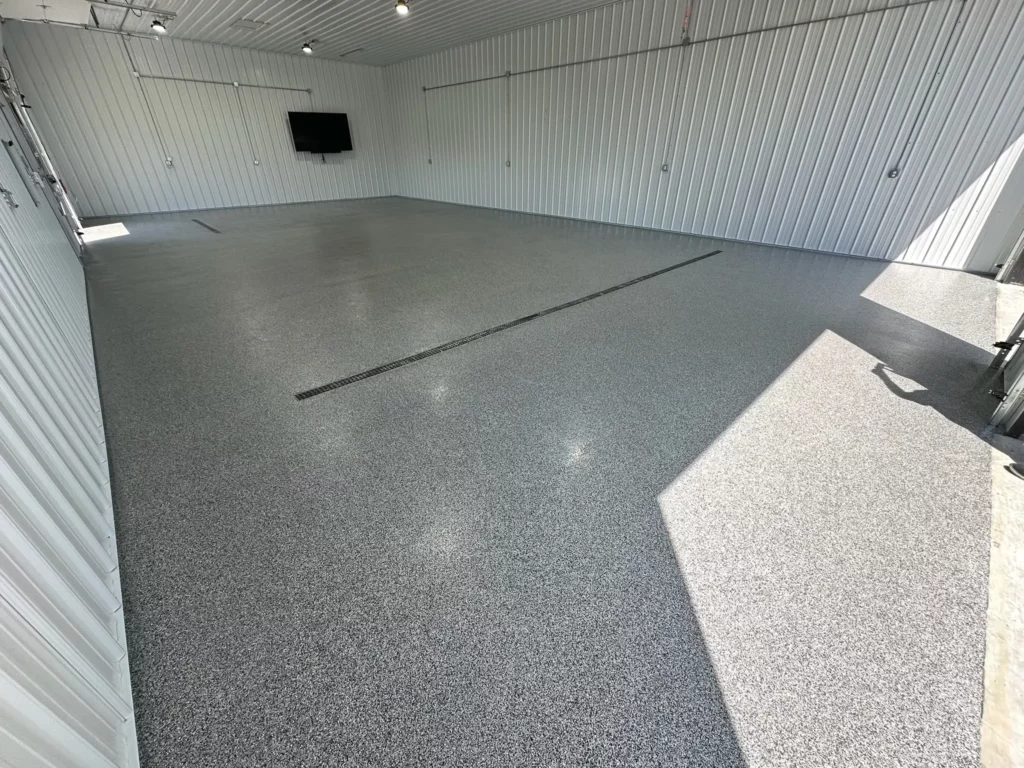
Forklift-Friendly Flooring Starts Beneath the Surface
The real strength of epoxy flooring depends on what’s under it. A strong epoxy system needs:
- Proper surface preparation (usually mechanical grinding or shot blasting)
- A clean, moisture-tested base slab
- Layered coats including primer, base coat, and topcoat
- Optional additives like quartz or aluminum oxide for grip and abrasion resistance
Think of epoxy like armor. Without a solid foundation, even the best armor won’t hold. That’s why professional installation—especially for industrial spaces—is non-negotiable.
Epoxy Thickness Matters
In industrial environments with heavy machinery or constant forklift use, epoxy floor coatings typically range from 1/8″ to 1/4″ thick. These thicker systems offer:
- Greater impact resistance
- Better load distribution
- Improved longevity under stress
Thinner DIY kits or low-solids epoxies simply won’t cut it for these kinds of applications. They’re more like paint than a true coating—and they’ll flake or wear out quickly.
Additional Enhancements for Industrial Durability
For added durability and functionality, epoxy floors can be customized with:
- Quartz broadcast systems for slip resistance and added strength
- Polyaspartic or urethane topcoats for UV stability and scratch protection
- Color-coded zones for safety and traffic guidance
- Chemical-resistant sealers in settings where oils or solvents are in play
These extras go a long way in extending the life of your floor and protecting your investment.
Real-World Applications: When Epoxy Meets Machinery
You’ll find heavy-duty epoxy flooring in:
- Manufacturing plants
- Warehouses and fulfillment centers
- Auto service facilities
- Cold storage and food processing areas
- Distribution hubs
These environments often have weight-bearing demands far beyond what your average concrete floor sees, but epoxy systems meet the challenge—especially when installed by experienced pros who understand what your space needs.
What About Vibration and Movement?
Some machinery doesn’t just sit—it vibrates, shifts, and creates friction. Epoxy floors with flexible topcoats or integrated shock-absorbing layers can help in these scenarios. These systems absorb micro-movement without cracking or delaminating.
This approach is especially useful near conveyor belts, hydraulic presses, or CNC machines that create repetitive motion.
Maintenance Still Matters
Even the toughest floor needs some TLC. To keep your epoxy floor performing under pressure:
- Clean regularly to remove debris that can scratch the surface
- Inspect high-traffic zones for early signs of wear
- Recoat as needed (typically every 7–10 years depending on use)
Luckily, maintenance is minimal—no waxing or buffing needed, and spills wipe up easily.
Epoxy vs. Other Heavy-Duty Flooring Options
How does epoxy stack up against other industrial flooring types?
- Polished concrete: Durable, but less resistant to chemicals and more prone to cracking under vibration.
- Tile or brick systems: Slippery and costly to maintain; grout lines are a problem area.
- Rubber flooring: Great for shock absorption but lacks load capacity.
- Epoxy: Checks the most boxes for strength, safety, chemical resistance, and ease of maintenance.
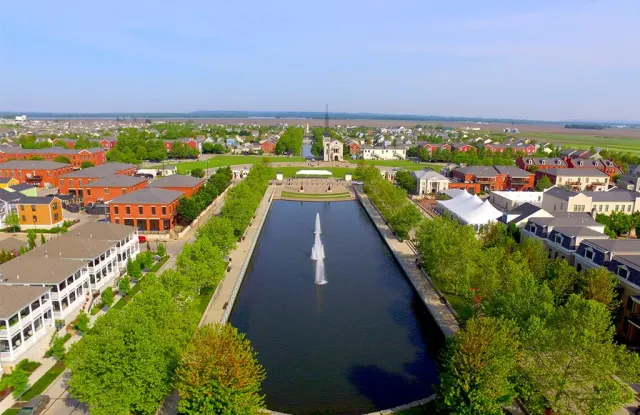
St. Charles Conditions = Local Insight Required
If you’ve ever walked through The Streets of St. Charles, you know this area blends sophistication and rugged charm. Industrial spaces here are no different—they need to look sharp and work hard. Seasonal moisture, temperature swings, and Midwest grit all play into how flooring should be installed and maintained.
That’s why choosing a local contractor like STL Coatings matters. They know what your facility faces day in and day out and can tailor your epoxy system for:
- Humidity and freeze-thaw cycles
- High traction and visual appeal
- Efficient installations with minimal business interruption
Cost vs. Value
Epoxy flooring for industrial use costs more upfront than a standard coating, but the long-term value is hard to beat. On average:
- Basic commercial epoxy systems: $4–$8 per sq ft
- Heavy-duty industrial epoxy systems: $8–$15 per sq ft
- Add-ons (quartz, topcoats, custom zones): Additional $1–$3 per sq ft
Compare that to the cost of shutdowns, repairs, or injury-related liability and you’ll see why epoxy is considered a smart long-term investment.
Final Thoughts
So, can epoxy flooring handle heavy machinery and forklifts? Absolutely—as long as you use the right materials, apply it properly, and maintain it periodically. For St. Charles industrial businesses, epoxy is a reliable, scalable solution that keeps your operation safe, clean, and efficient.
From chemical resistance to load-bearing toughness, epoxy does it all. And with STL Coatings as your partner, you can rest assured that your floors are ready for whatever drives, rolls, or rumbles across them.
Because when your floors are built like your business—strong, steady, and built to last—everything else moves a little smoother.