Warehouses are the backbone of countless businesses in St. Louis, handling everything from logistics and distribution to manufacturing and storage. With heavy equipment, constant foot traffic, and daily wear and tear, choosing the right flooring isn’t just a matter of aesthetics—it’s about durability, safety, and efficiency. So the question is, what is the best epoxy flooring for St. Louis warehouses?
If you’re considering epoxy for your warehouse, STL Coatings offers expert insights and installation services to help you make the right decision. Now, let’s break down the best epoxy flooring options for St. Louis warehouses and why they matter.
Why Epoxy Flooring is Ideal for Warehouses
Warehouses demand flooring that can handle extreme conditions, and epoxy fits the bill perfectly. Here’s why:
- Durability: Epoxy creates a hard, impact-resistant surface that withstands forklifts, heavy machinery, and dropped tools.
- Chemical Resistance: Spills from oils, solvents, and industrial chemicals won’t damage or stain properly installed epoxy flooring.
- Safety Features: Slip-resistant additives can enhance traction, reducing workplace accidents.
- Ease of Maintenance: Epoxy’s seamless surface makes it easy to clean, minimizing downtime for maintenance.
- Cost-Effective Longevity: Compared to traditional concrete or tile, epoxy lasts longer and requires fewer repairs.
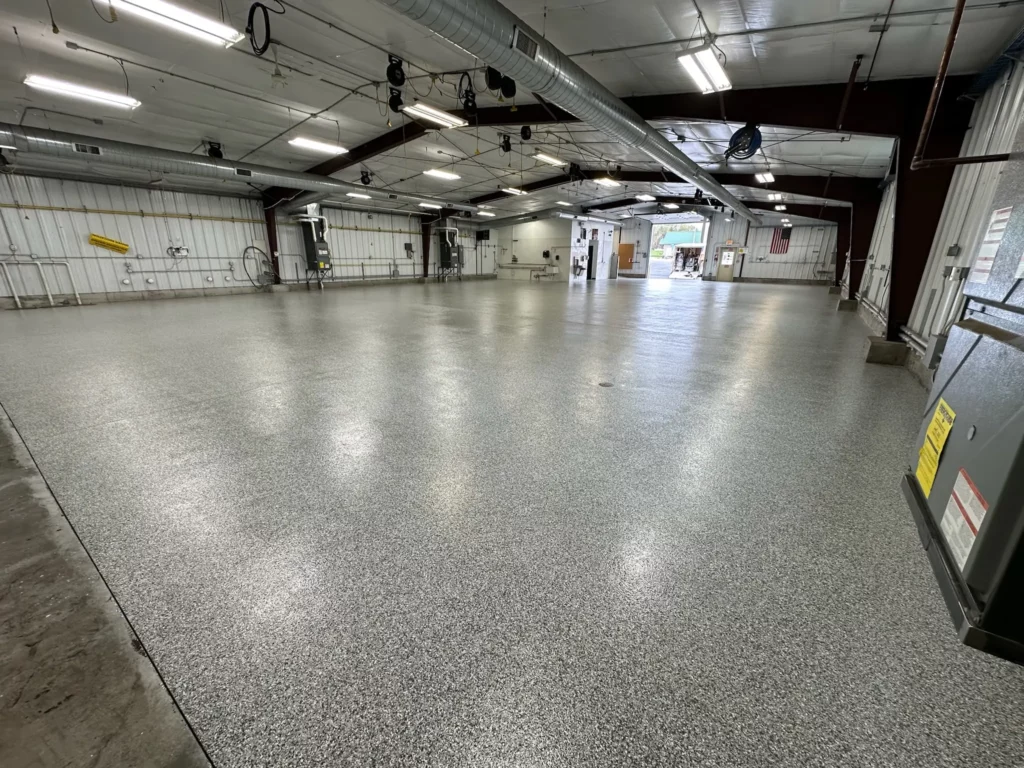
The Best Epoxy Flooring Options for Warehouses
1. 100% Solid Epoxy Flooring
If longevity is the priority, 100% solid epoxy is the gold standard. This formulation provides a thick, ultra-durable layer that can withstand extreme conditions and heavy traffic without breaking down.
Best For:
- Warehouses with forklift and vehicle traffic
- Manufacturing plants
- Heavy-duty storage facilities
Pros:
- Highest durability and impact resistance
- No solvents, meaning no shrinkage during curing
- Long lifespan with minimal maintenance
Cons:
- Requires professional installation
- Higher upfront cost
2. Epoxy with Quartz Additives
Quartz-enhanced epoxy flooring offers additional strength and slip resistance, making it a great choice for warehouses where spills or fine dust particles could create hazards.
Best For:
- Facilities with frequent liquid spills
- Warehouses requiring extra traction for safety
Pros:
- Enhanced traction for worker safety
- Extra abrasion resistance
- Aesthetic appeal with quartz blends
Cons:
- Can be slightly more expensive due to added materials
- Requires skilled application
3. Epoxy Flake Flooring
Flake flooring is a popular choice for warehouse spaces that need both functionality and a professional appearance. The addition of decorative flakes increases surface grip while offering a customizable look.
Best For:
- Showroom warehouses
- Facilities requiring high-visibility safety markings
- Workspaces where aesthetics matter
Pros:
- Customizable colors and patterns
- Slip-resistant surface
- Conceals minor imperfections in the substrate
Cons:
- Requires a protective topcoat
- More intricate installation process
4. Metallic Epoxy Flooring
While not as common in traditional warehouse spaces, metallic epoxy is an option for businesses that want a high-end, durable flooring solution. Its reflective properties can even improve lighting conditions, reducing the need for excessive artificial light.
Best For:
- Warehouses with a customer-facing component
- High-end manufacturing facilities
Pros:
- Visually striking appearance
- Can improve brightness in workspaces
- Extremely durable
Cons:
- Higher cost than standard epoxy coatings
- Not necessary for most industrial environments
How to Choose the Right Epoxy Flooring for Your Warehouse
Choosing the best epoxy flooring for your warehouse depends on several factors:
- Traffic Levels: High-traffic warehouses need 100% solid epoxy for maximum durability.
- Slip Resistance Needs: If spills or dust accumulation are concerns, opt for quartz or flake-enhanced epoxy.
- Budget Considerations: While epoxy is cost-effective long-term, initial installation costs vary by type.
- Aesthetic Preferences: If your warehouse has a showroom component, consider flake or metallic finishes for a polished look.
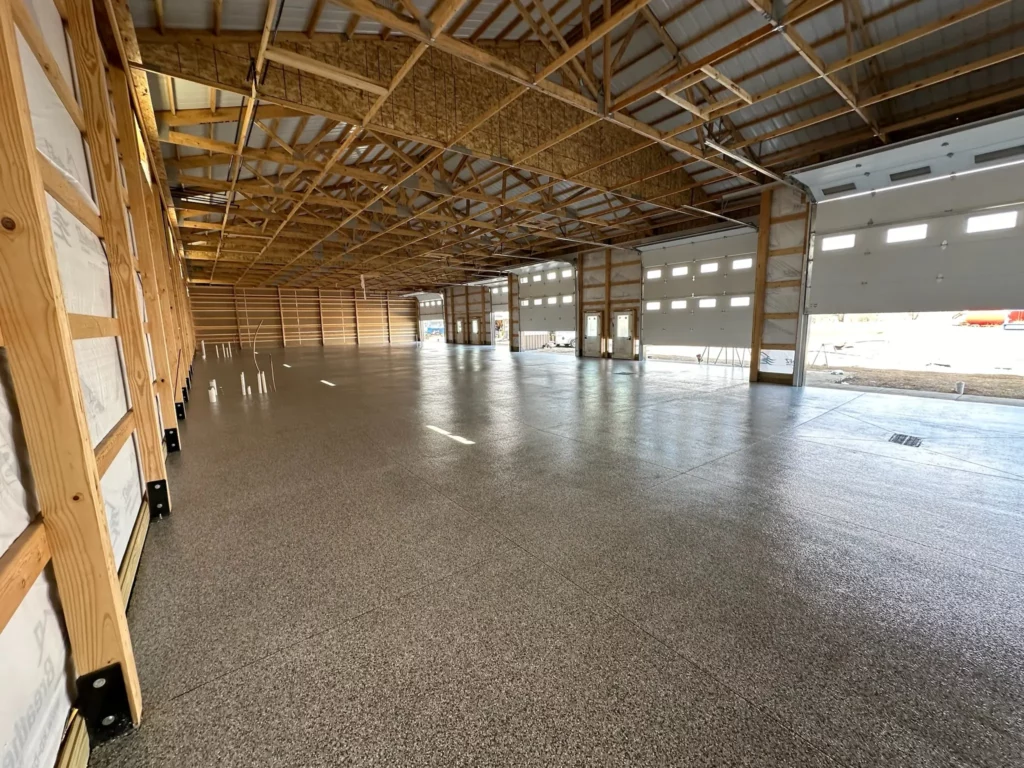
Installation Considerations for Warehouse Epoxy Flooring
Installing epoxy in a warehouse setting requires precision and planning. Here’s what to expect:
- Surface Preparation: The existing concrete floor must be cleaned, repaired, and mechanically ground for proper epoxy adhesion.
- Primer Application: A high-quality primer helps the epoxy bond securely to the concrete.
- Base Coat Application: Depending on the type of epoxy chosen, this layer provides durability and impact resistance.
- Optional Additives: Quartz, flakes, or slip-resistant aggregates can be added to improve functionality.
- Protective Topcoat: A final sealer enhances longevity and stain resistance.
- Curing Time: Epoxy requires 24-72 hours to fully cure before heavy equipment can be used.
Warehouse Flooring That Works as Hard as You Do
A well-installed epoxy floor makes warehouse operations smoother, but just like any good system, it’s only as strong as its foundation. Think about it like The Magic House in St. Louis. If you’ve ever been there, you know it’s a place designed to handle an endless stream of excited kids running, jumping, and testing the limits of every hands-on exhibit. And yet, year after year, the place holds up beautifully—because it was built with durability in mind. A well-chosen epoxy floor does the same thing for your warehouse, keeping things running efficiently no matter how much action it sees. If you haven’t been in a while, you can check out everything The Magic House has to offer here.
Final Thoughts
Epoxy flooring is one of the best investments you can make for your St. Louis warehouse. Whether you need heavy-duty protection, added slip resistance, or an aesthetic upgrade, there’s an epoxy solution that fits your needs.
For expert advice and professional installation, STL Coatings has the experience and resources to ensure you get a flooring solution that lasts.
A great warehouse starts with a strong foundation—just like The Magic House, it’s all about creating something built to last and handle whatever comes its way.